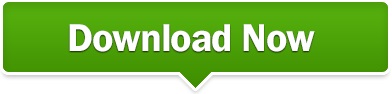
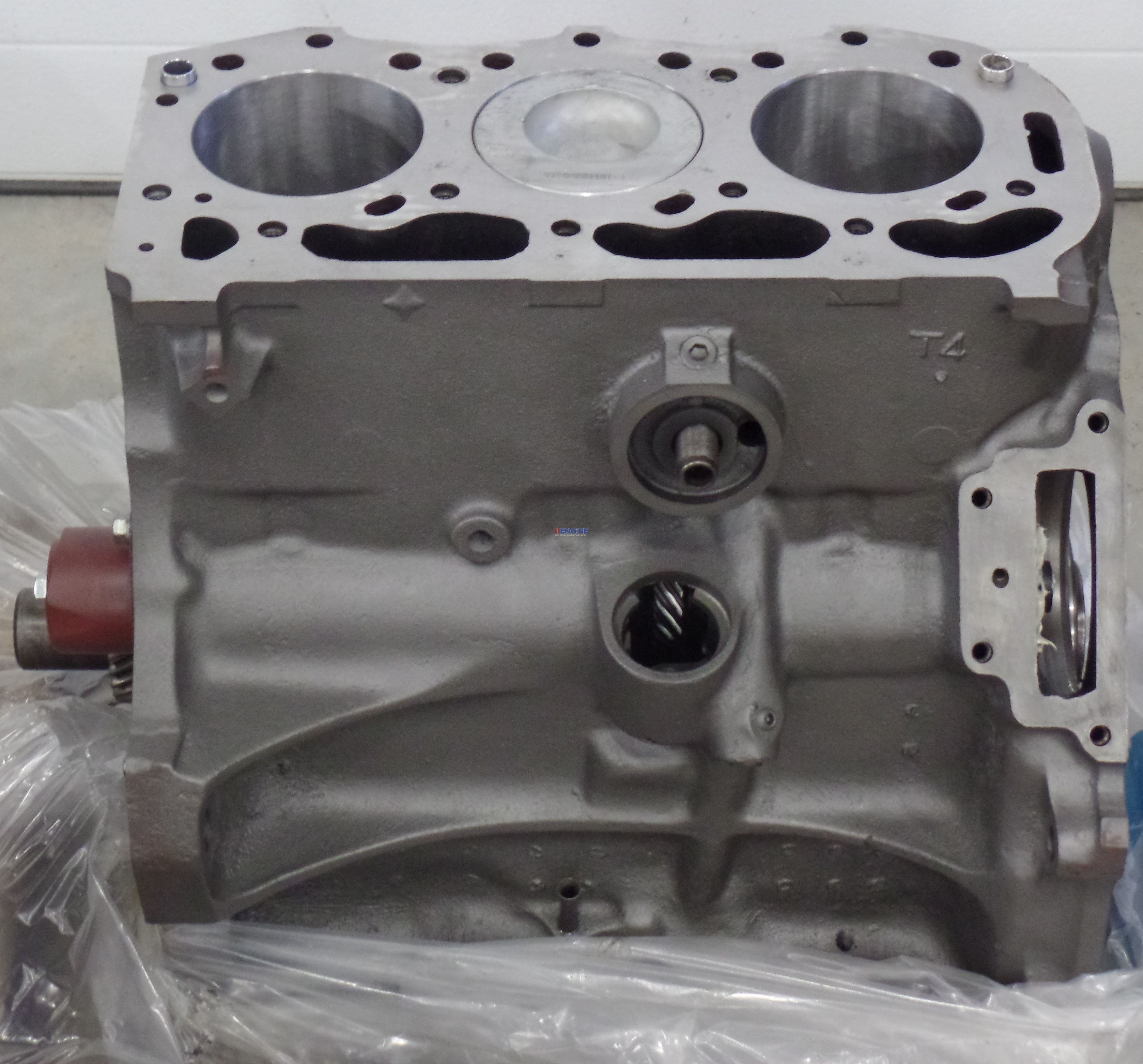
Specialized knowledge was necessary to determine the composition of melted samples, so the company brought in an experienced foundry worker from another company, allowing it to make the changeover to internal production. The composition of malleable cast iron differs from regular cast iron, and because there was no quick way to analyze the composition, adjusting it was very difficult. The company initially outsourced production of malleable parts for the chassis and drive system, but later changed to in-house production.
#TOYOTA ENGINE BLOCK CASTING NUMBERS TRIAL#
It was through this kind of repeated trial and error that the Automotive Department's research laboratory developed the basic technology necessary for manufacturing automobiles. After asking the research laboratory of the Steelmaking Department to perform some materials tests, the team determined that by significantly increasing the amount of cutting stock, they could almost completely eliminate the number of defect molds. The team discovered that by further machining away the inside of the cylinders the pits would disappear. A similar problem occurred at around the time the Model G1 truck was launched in November 1935. After turning out ten cast cylinder blocks, only one or two were making it through the machining process. However, when machine boring the inside of the cylinders, small pits 4 were forming, making the cylinders unfit for use. 3Ī mold for the cylinder block was finally completed in August 1934. Furthermore, because the single oil core for the hollow portion of the three cylinders and crank room was so large and heavy, and because it was so difficult to make, it was separated lengthwise into two in the direction of the cylinder arrangement.
#TOYOTA ENGINE BLOCK CASTING NUMBERS HOW TO#
The ratio of oil to sand, firing temperature and time were all individually adjusted until the team gained a good understanding of how to make the oil cores. The oil-sand mix was then put into a wooden mold, and fired in a ceramics kiln. The oil was mixed in with sand taken from a beach on the Chita Peninsula in Aichi Prefecture. The team procured tung oil, which is applied to paper lanterns and umbrellas to waterproof them, from a paper umbrella maker in Gifu, to use as the drying oil to be mixed in with the sand. casting-related journals such as Foundry and Foundry Trade Journal, but it was the first time that they had seen the real thing. The R&D team had gained some knowledge about oil cores from U.S. But the core-making had its own difficulties. Earlier in March that year, Director Risaburo Oshima had returned to Japan from the United States and brought with him some oil cores no larger than one's little finger, allowing the R&D team to manufacture oil cores for use in casting the Type A Engine cylinder blocks. Subsequently, in May 1934, the research laboratory began making prototype cylinder block molds. These efforts resulted in the R&D personnel being able to replicate cylinder blocks for the A Engine of the same special composition (nickel-chromium cast iron) as the Chevrolet cylinder blocks. In order to do this, someone capable of analyzing the alloy cast iron composition was deployed to the foundry. They then analyzed the composition of the prototype molds, repeating the whole process as necessary. The R&D personnel analyzed the composition of the cylinder blocks from a Chevrolet engine, and based on the results of their analysis created prototype molds using the electric furnace.
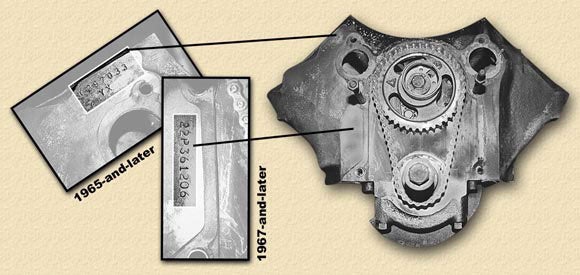
The purpose was to create alloy cast iron for cylinder blocks. In conjunction with the installation of the Daido electric furnace at Toyoda Automatic Loom Works, Kiichiro instructed the R&D personnel to conduct further research into electric furnace-produced cast iron. At the time, producing cast iron using an electric furnace was unknown territory even for electric furnace manufacturers. (now Daido Steel Co., Ltd.) for a 800 kVA 3-ton electric arc furnace, it is said that Daido responded by saying that they don't manufacture electric furnaces to melt cast iron.
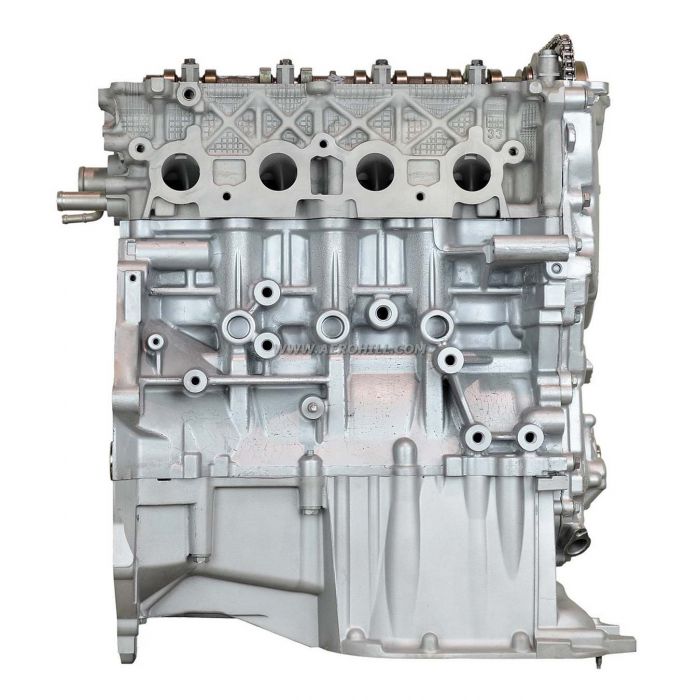
2 Later, in 1933 when the company placed an order with Daido Electric Steel Manufacturing Co., Ltd. 1Īccording to Umeji Harada, who had been a foundry worker at Toyoda Automatic Loom Works since its earliest days, the company was the first in Japan to produce cast iron using an electric furnace. Later, in 1930, alloy cast iron produced by the electric furnace was used in parts for the spinning machines. Cast iron produced by an electric furnace was harder and had greater tensile strength than that produced by a cupola furnace in other words, the cast metal exhibited superior mechanical properties. Not long after Toyoda Automatic Loom Works began operations in 1927, the company installed a 1.5-ton electric arc furnace, as instructed by Kiichiro.
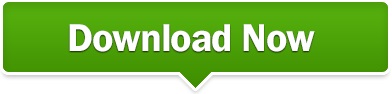